Case Study: Monitoring Mitsubishi Paper Production
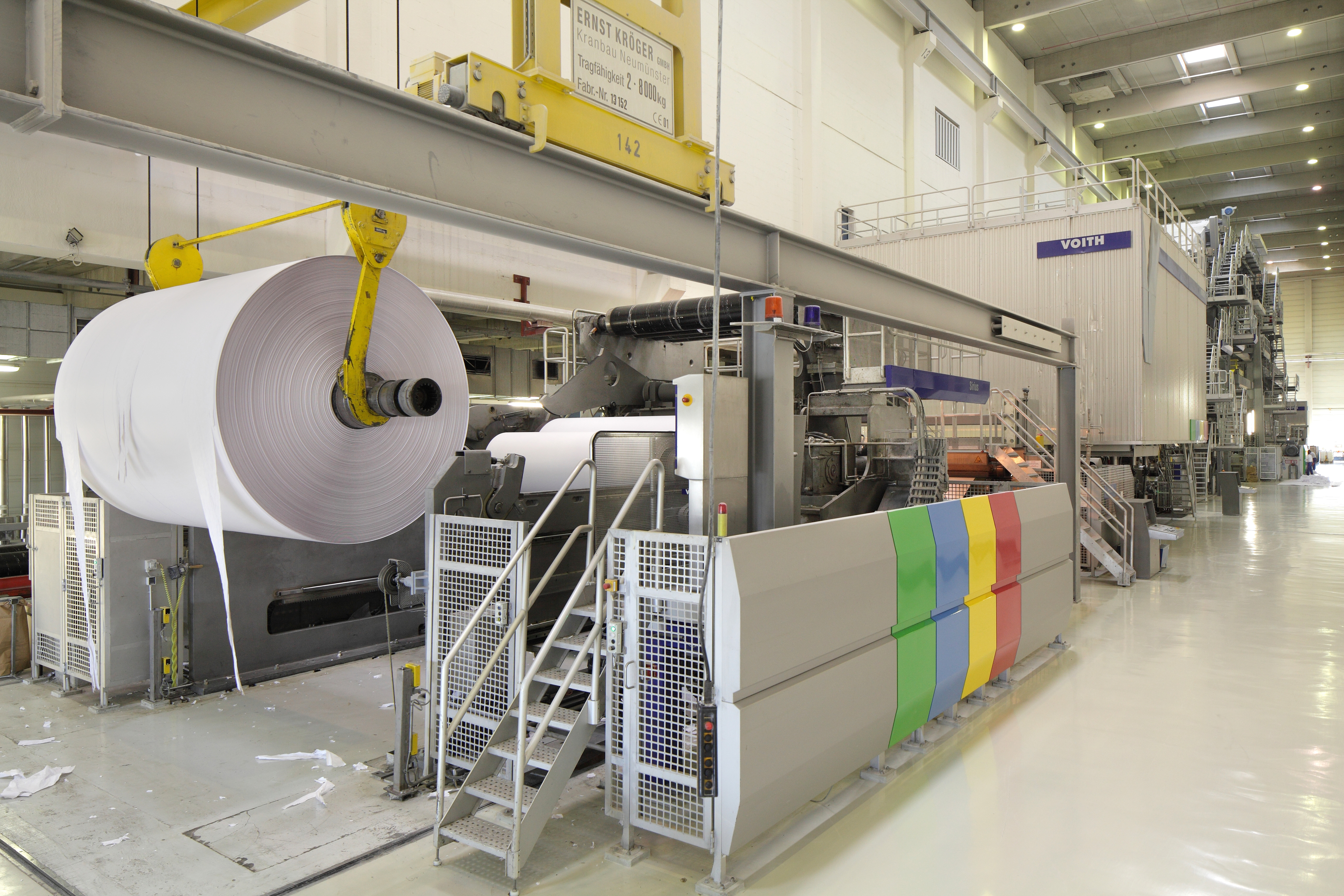
Mitsubishi HiTec Paper is one of the most prominent specialty paper manufacturers worldwide. Headquartered in Germany, Mitsubishi has been making paper since 1799. With over 500 employees, two paper machines and five coating machines, they manufacture approximately 150,000 tons of specialty paper every year. Their product portfolio encompasses inkjet paper, thermal paper, carbonless paper, label paper and protection paper for flexible packaging. Since the factory produces a large amount of paper, any system failure would result in significant economic loss for the company. As a result, the production equipment at the factory has been fitted with an ungrounded power supply and a Bender insulation monitoring device (IMD).
The advantage of an ungrounded system being used in the factory is that there is no connection between power source (transformer) and earth. This means that the electrical installations still function in the event of a single ground fault. In a classic grounded system, the fault would trip a protective device, shutting off the power supply and halting production. Insulation faults such as this can often be traced back to wet conditions, moisture or mechanical/electrical loads, all of which are high risk factors in a paper factory which uses a lot of water in its processes.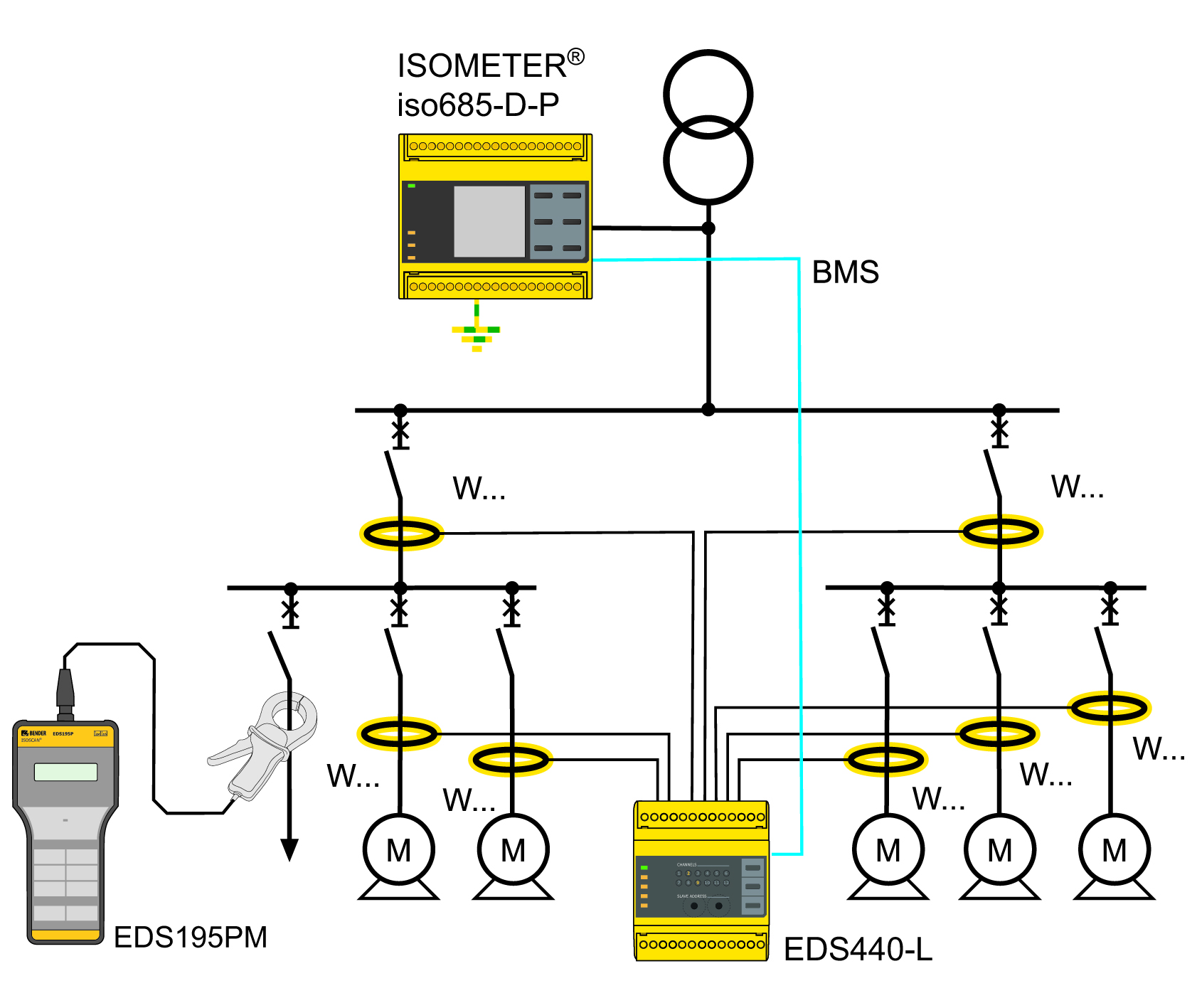
Both of these potentially destructive problems were solved with a single Bender device: the latest iso685-D-P insulation measuring device combined with the portable EDS3090. The iso685-D-P identifies and reports insulation faults before they become critical so that they can be remedied in time to prevent halts in production. The EDS3090 is then paired with the iso685-D-P in order to quickly and automatically pinpoint the exact location of the fault. Service personnel are then notified of faults in advance by a pre-alarm feature. This prevents critical production interruptions, which are especially disastrous for the paper industry because of the time it takes to get the paper machines back up and running.
Thanks to the addition of the iso685-D-P insulation monitoring device with an integrated locating current injector and the EDS insulation fault location system, insulation faults can now be identified earlier and with a higher degree of safety. This significantly lowers maintenance costs and dramatically improves equipment availability.
For more information about this application or to learn more about Bender technology related to your specific application, contact our team of experts.
This article is for informational purposes only. Bender provides the information "as is" without warranty and is not responsible for its accuracy or reliability. No warranties are given regarding its suitability for any specific circumstances.