Keeping electrical railways safe
Ensuring safety in rolling stock electrical storage and propulsion systems while maintaining the highest possible availability of equipment depends on identifying and dealing with faults at the earliest opportunity.
Operational equipment that cannot tolerate shutdown or failure is often designed as an ungrounded electrical network. This allows systems to continue running even if an insulation fault occurs, as eliminating an earth connection ensures the first fault current is typically not at a dangerous level, so it doesn’t cut out by tripping the circuit breaker. Instead, the system delivers an audio or visual alarm that ensures the fault is addressed before it escalates and causes problems.
A second fault on the same system changes the situation, because the fault current may reach a level where it could prove harmful or pose a fire threat. That makes it crucial to identify and rectify a first fault while the system can continue to operate.
Many critical ‘no fail’ industrial applications employ ungrounded systems, where unplanned shutdowns or failures can jeopardize safety and incur financial penalties and reputational damage.
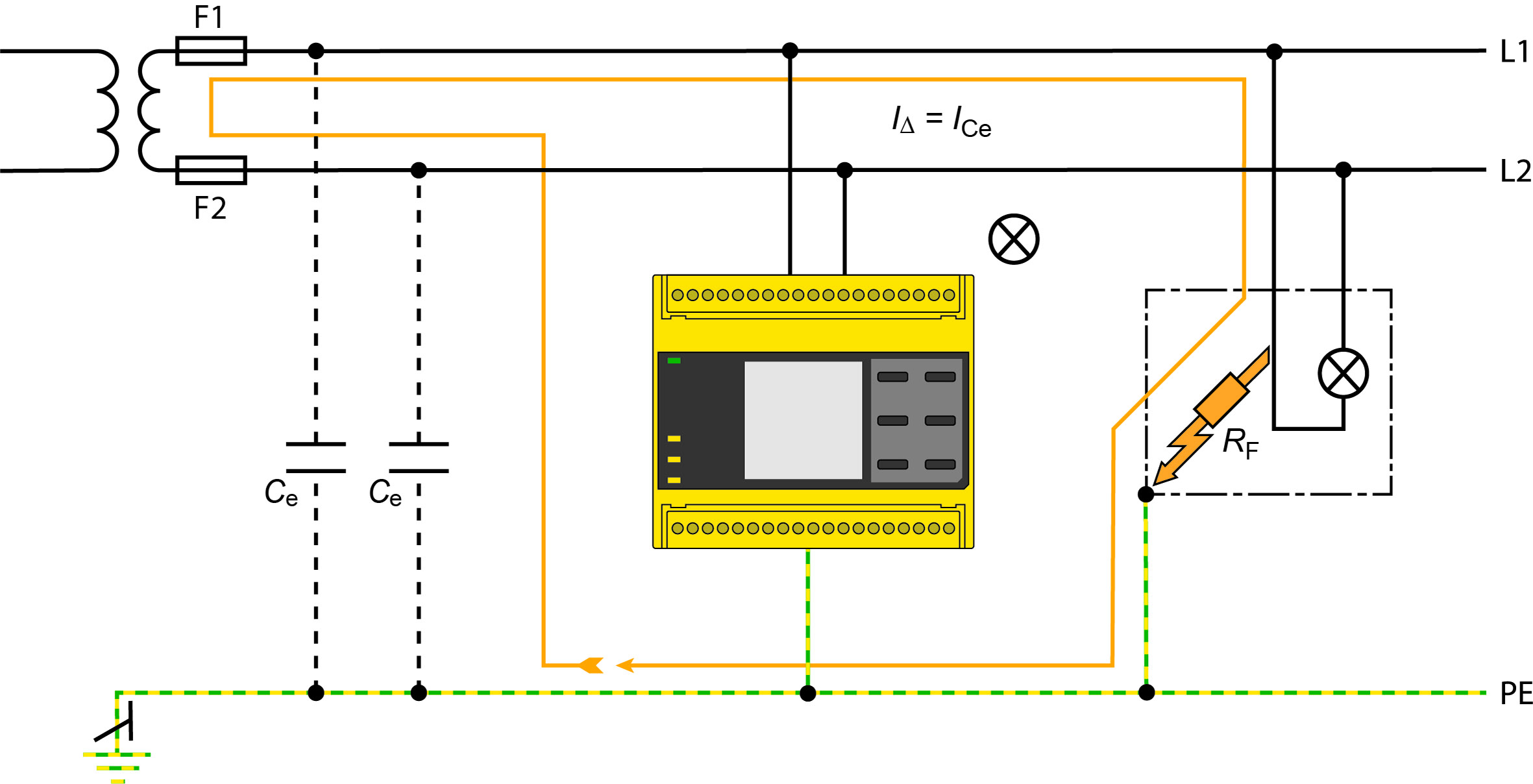

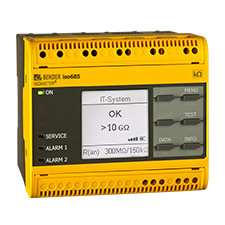
Real-time monitoring
The latest trends in propulsion systems in rolling stock have increased the complexity and the potential for earth faults in electrical networks. It is therefore essential to have a real-time overview of the condition and identify possible threats as soon as they emerge, maintaining plant availability and enabling predictive and preventive maintenance.
Continuous monitoring with an insulation monitoring device (IMD) indicates critical values and the development of issues even before an alarm is sounded, providing a real- time check on system health.
These values forewarn of developing failure, providing system information and allowing corrective action before faults become critical. This reduces unplanned downtime and maintains availability of assets at a high level.
However, keeping the system running after an insulation fault comes with a downside. In a grounded electrical network, a fault normally results in tripping a circuit breaker, clearly identifying the branch where the fault has occurred. This is not the case in ungrounded networks. Typically, on an ungrounded circuit maintenance personnel must try to identify the fault by disconnecting parts of the network and checking the reaction of the resistance value shown on the IMD.
Depending on size, the time and effort taken to identify the fault can be huge because in addition to disconnecting parts of the network, the maintenance team must wait for the measurement cycle of the connected IMDs. Depending on the capacity in the network this could add up to several minutes per feeder. Separation and reconnection of cables comes with the risk of touching a live working system. On a train these procedures may also impact other maintenance processes due to an interruption of the power supply for lighting or power sockets.
Fast fault identification
First faults can be identified using an insulation fault location system (IFLS) to technically locate earth faults during normal operation without interrupting any power supplies. Once a train is equipped with an IFLS the location process can start immediately after a fault occurs. The system feeds a current between phase and ground into the network which is equipped with current transformers and the location device. The locating current can be detected in the faulty feeder by the transformer, which then communicates to the detection unit.
As an alternative to an installed IFLS, a mobile pulse generator can be used in combination with a handheld device. This reduces the time taken to identify faults, which means increased availability of the train.
Generally, it is rare to find a completely fault-free electrical system in any location, especially rolling stock subject to high operational demands. Having an effective system design incorporating fault identification and location systems is the next best thing – reducing downtime and maintaining availability of vital equipment and rail services.
For more information about this application or to learn more about Bender technology related to your specific application, contact our team of experts.
This article is for informational purposes only. Bender provides the information "as is" without warranty and is not responsible for its accuracy or reliability. No warranties are given regarding its suitability for any specific circumstances.