Pinpointing core to earth faults for a safer rail network
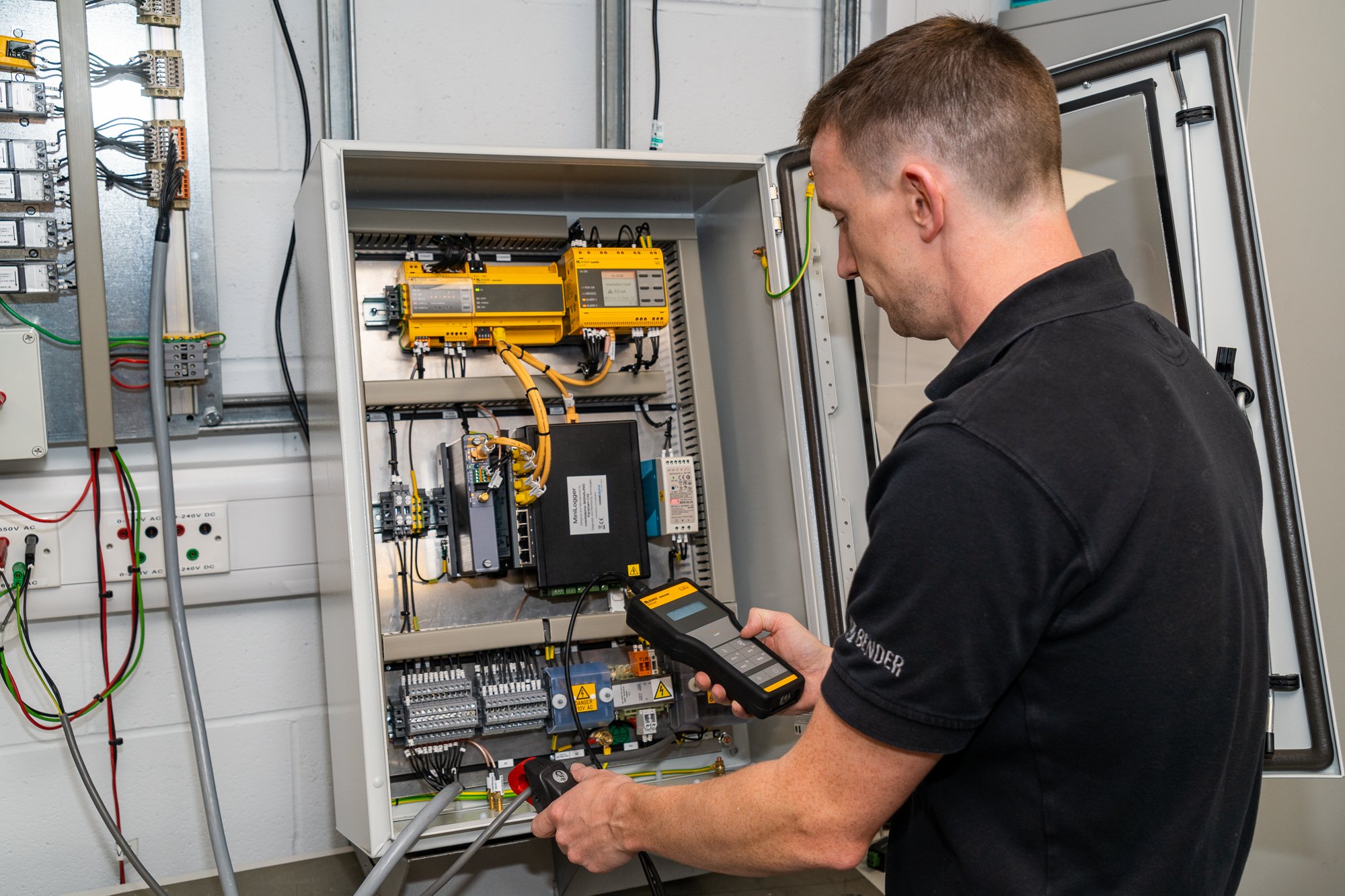
Railways require safe, reliable power systems to support signals, points and communications infrastructure.
Trackside equipment must be protected from failure, and with thousands of miles of track to maintain, Network Rail demands maximum visibility to assess the health and condition of its infrastructure.
UK rail networks are subject to harsh operating conditions and incidents of theft, accidental damage and degradation. Finding and locating faults is challenging, currently requiring rail personnel to spend thousands of hours trackside inspecting and locating failing cable.
Boots off ballast
The major drive to get ‘boots off ballast’ is supported by earlier identification of emerging power system faults and more accurate fault location technology. This gives a longer window to rectify faults and enables predictive and preventive maintenance rather than reactive maintenance, offering opportunities to deal with faults before they become critical.
More effective fault finding translates into fewer train delays and an improved customer service with reduced associated costs for train operators through fewer penalties.
Most rail signalling power supply issues (more than 80%) result from core-to-earth faults where damage or deterioration of a cable or its insulating covering will eventually lead to failure, impacting on safety and the efficient operation of rail services.
Rail Signalling Power Monitoring systems have been the principal method of tracking and locating faults on the rail signalling power network for two decades. However, less critical emerging faults at lower intervention/insulation limits are more difficult to track and pinpoint.
Network Rail regulation NR/L3/SIGELP/50001 requires an increase in intervention windows. Faults identified at critical stages (20 kΩ or lower) require immediate intervention within 24 hours. Advanced monitoring and insulation fault location at up to 100kΩ increases intervention time, enabling fault identification within a prescribed 6-week window. More importantly, it also offers the option of dealing with the fault over a longer timescale through planned and predictive maintenance.
New generation multi-tier RS4 Rail Signalling Power Monitoring offers increased sensitivity for first fault location and remote condition monitoring of core-to-earth failure of Network Rail signalling IT power systems. It was developed collaboratively with Network Rail (NR) in response to new standards designed to reduce maintenance, reduce infrastructure and service failures and improve staff safety by minimising trackside intervention and ‘boots on ballast’.
RS4 is compliant with Network Rail’s Insulation Monitoring and Fault Location requirements. It provides continuous monitoring of ‘live’ rail signal power systems and pinpoints the locations of cable or earth faults without the need to power down systems. It incorporates 3G/4G enabled data loggers equipped for real-time direct communication with Network Rail’s Intelligent Infrastructure. Data from the continuous monitoring is supplied in weekly reports delivered directly to Network Rail and can be supplemented with further detail and analysis to create a holistic picture of the network.
Manual cable testing on a 5-year cycle NR/L2/SIGELP/50000 continues to be a requirement, but RS4 is a key step forward in enabling Network Rail to move from periodic testing to a real-time condition-based approach through continuous testing.
Multi-tier core-to-earth fault location
RS4 is designed to satisfy Network Rail Tier 1, 2 and 3 fault location requirements, employing tried and trusted Bender measuring technology with increased sensitivity for improved feeder first fault location. RS4 delivers continuous monitoring and analysis capabilities unachievable with previous technology. The lower the resistance, the more serious the fault; the limit at which faults could previously be located was 20kΩ – which indicated a fault requiring urgent attention. Higher resistance levels around 100kΩ are early warnings of cable insulation degradation but they were previously almost impossible to locate.
Insulation monitoring combines with an integrated fault locating current injector, pinpointing the fault locations on miles of networked cables. It also measures capacitance, voltage and frequency offering rail engineers a holistic picture of cable health enabling emerging problems to be identified, providing a rich data set that meets the requirements of multi-tier standard NR/L2/SIGELP/27725.
How does monitoring and fault location work?
RS4 narrows the location of core-to-earth high resistance faults to specific short lengths of the power supply cable using fixed technology. This fault location can be carried out without cutting the power, while the system is online/running, and complies with the IEC 61557-9 definition of an iFLS/ fault location system.
Time Domain Reflectometry - a supplementary fault location technology sometimes confused with iFLS - is effective only on rare core-to-core short circuit or open circuit faults when a power failure has occurred and is already causing train delays. RS4 continually monitors insulation resistance (IR) to show real-time status of the power system. When IR drops, the system records the fault, sending a test current signal into the system which is pulled to earth at the point of fault.
A portable earth fault location system EDS3090 (known as ‘the Bender Wand’) precisely locates feeder earth faults line-side, allowing the repair process to be carried out more quickly with minimal disruption. The handheld unit pinpoints a network earth fault to a specific cable or transformer by detecting the test signal from Bender devices and does not require the cable or transformer to be disconnected. EDS3090 clamps to the cable to carry out the evaluation, enabling spot checks to discover whether a fault is present.
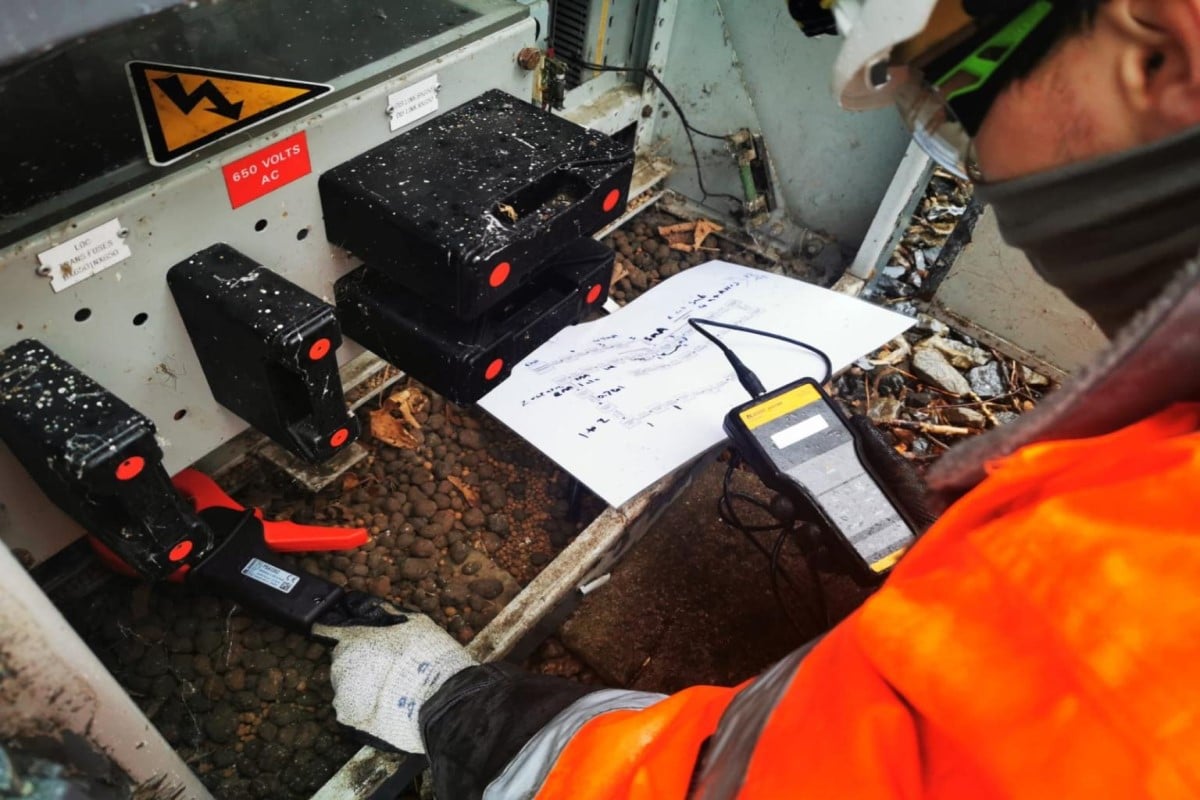
Upgrading existing rail signalling equipment
Existing RS2/RS3 installations can be upgraded to an RS4. This is important for Network Rail as there are more than 1,000 earlier generation Bender systems installed.
Bender ensure cost-effective continuation for legacy equipment that is compatible with Network Rail’s Intelligent Infrastructure and delivers remote condition monitoring through the GSM 3G/4G enabled data loggers.
Network Rail has formally approved Bender UK’s next generation RS4 Rail Signalling Power Protection system at Tier 3 level, and testing is on track for Tier 2 and Tier 1 installations.
The Network Rail full approval certificate (PA05/04750) covers the Tier 3 version of the RS4 devices. The RS4 Tier3 PADs number on the Network Rail accepted products database is 0086/001406.
Full approval certification of RS4 units makes specification of the equipment simple for Network Rail and its partners who are committed to delivering the multiple-tier smart cable insulation monitoring and fault location that is required to reduce rail downtime and achieve the highest operational standards.
RS4 Tier 3
The Network Rail certified Tier 3 solution is designed to comply with NR/L2/SIGELP/27725. It offers an overall system insulation resistance level measurement that includes multiple feeder systems and signal power supplies where each feeder is fed from either a common or individual isolation transformer. Increased sensitivity improves fault location from 20kΩ to 100KΩ and higher, on IT AC/DC systems (depending on system capacitance).
Tier 3 employs patented Bender AMP technology and current measurement type-A CTs (current transformers) for fault location. AMP is based on a special clocked measuring voltage controlled by a micro-controller and adapts automatically to prevailing system conditions. Software-based evaluation means system leakage currents causing interference on evaluation circuits can be differentiated from the measured variable proportionate to the insulation resistance in ohms.
RS4 Tier 2
The Tier 2 solution enables complex individual feeder measurements and delivers enhanced monitoring and measurement capabilities over the RS4 Tier 3. This compliant solution offers increased system availability by providing the full insulation resistance (IR) levels of individual feeders, in addition to overall system level IR.
Tier 2 compliance is achieved by the use of additional system components. These include Bender Type B current transformers (CTs), the EDS440WNR evaluator, Bender COM465IP condition monitors to enable complex individual feeder measurements. Comprehensive data readings and information on cable health enables operators to have a clearer overall assessment of the condition of the rail signal power system.
RS4 Tier 2 delivers the same functionalities as the Tier 1 solution at PSP level and is fully upgradable to deliver a Tier 1 solution with the addition of an EDS440WNR fault evaluator and Type B CT at FSP (Functional Supply Point) level.
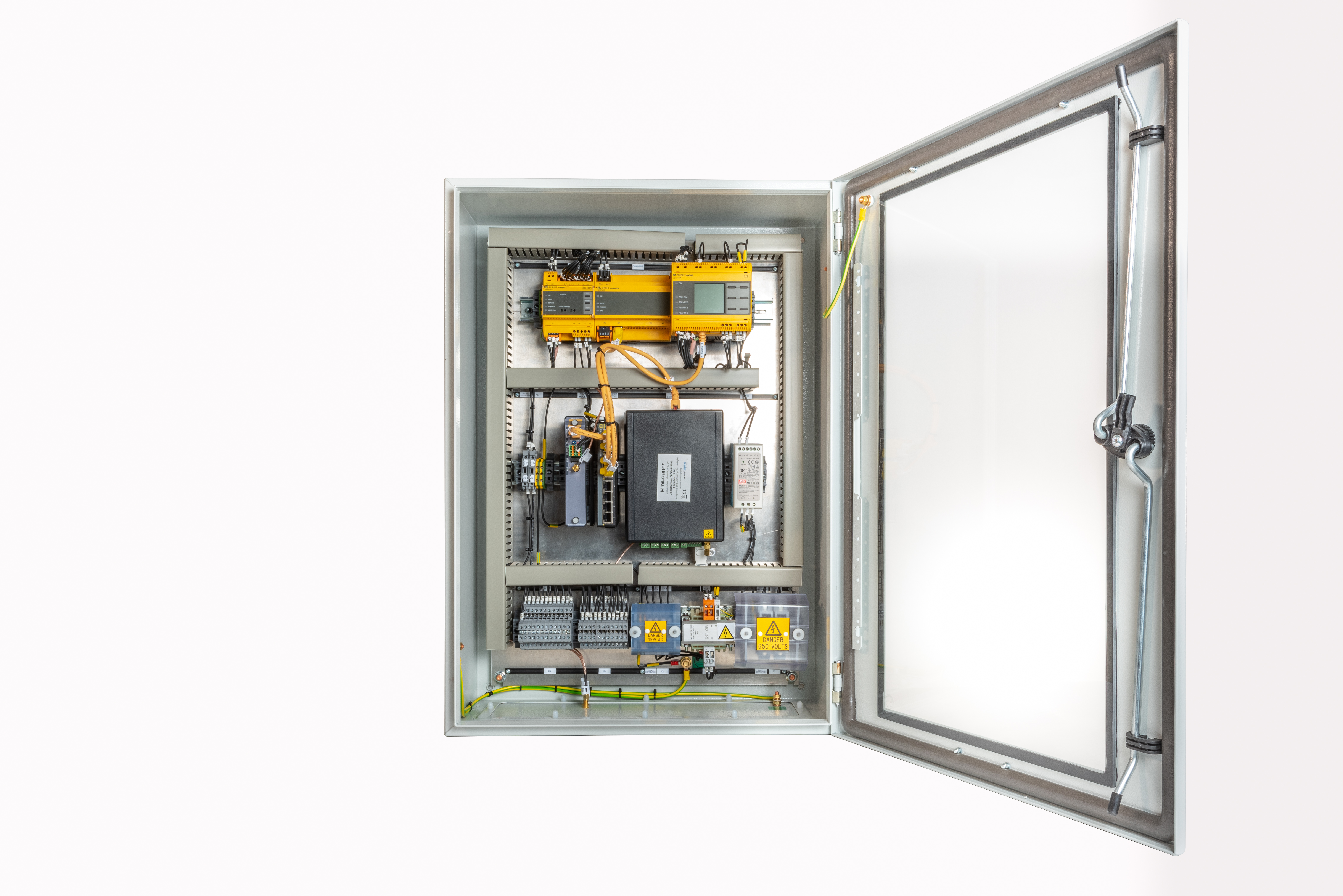
RS4 Tier 1
The Tier 1 is the most advanced solution. It delivers the highest level of granularity of a monitored signalling power system and offers insulation resistance measurement to cable subsection level and FSP levels, in addition to all the advantages of the Tier 2 system.
Incorporating an earth fault evaluator (EDS440WNR) and Type B current transformers (CTs) inside FSPs, it evaluates and locates fault sources and provides full insulation resistance measurement of the system and individual feeders, monitoring individual subsections of cable and FSP.
Tier 1 allows for the overall and individual feeder IR measurement using the Class II compliant field/FSP equipment to provide IR readings of each cable sub section. Tier 1 eliminates the need for earth connection, with all trackside equipment fully integrated into existing FSP enclosures. Importantly, it is able to measure the IR within the FSP switchgear where most faults occur.
Available in 650v mains or 110v supply option, Tier 1 is retrofittable to Class II and Class 1 equipment, while data and communications options can be customised to suit specific projects and customer requirements.
For more information about this application or to learn more about Bender technology related to your specific application, contact our team of experts.
This article is for informational purposes only. Bender provides the information "as is" without warranty and is not responsible for its accuracy or reliability. No warranties are given regarding its suitability for any specific circumstances.